How to save energy and reduce consumption in asphalt mixing plant from the perspective of raw materials?
1. Adjust the moisture content and size of stone
The asphalt mixer needs to heat and dry raw materials, and a large amount of fuel is consumed in the heating process of the machine. The stone itself contains more water, especially the fine aggregate of 0-0.27, which has strong water absorption. If the water content of the stone is too high, it will cause a lot of waste of resources. According to statistics, the energy consumption of asphalt mixer will increase by about 12% for each percentage point increase in the moisture content of stone. Therefore, in order to save energy, managers should pay attention to adjusting the moisture content of raw materials and reduce the moisture content of materials by optimizing the quality of raw materials and improving the environment of the stacking site. Specifically, the material quality inspection link can be added. Unqualified raw materials should be resolutely resisted, and they must not be made up to affect subsequent production. Considering environmental factors, warehouse canopy, seepage ditch, drainage ditch and other drainage facilities can be added to improve the drainage capacity of the site and reduce the moisture content of materials to the greatest extent, so as to improve the working efficiency of asphalt mixer and reduce fuel consumption.
The diameter of the stone will also affect the operation efficiency of the asphalt mixer. If the stone particle size is too large, the mixing efficiency of the mixer will be reduced. If the hole diameter qualified rate of the stone is less than 80%, the operation efficiency of the mixer will be reduced by 20%. If the hole diameter qualified rate is less than 60%, the efficiency of the mixer will be reduced by more than 55%, which will cause a lot of energy consumption, When the aperture error of stone is too large, it may lead to the overflow of raw materials, which will cause greater losses. Therefore, it is very important to control the aperture of raw materials.
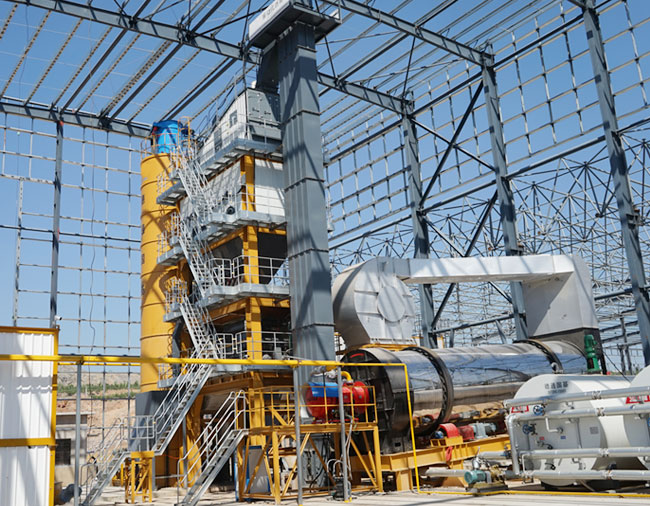
2. Select appropriate fuel
In order to improve the mixing efficiency of asphalt mixer, the mixing plant needs to select appropriate fuel. At present, the more common fuels are liquid fuel and gas fuel, and very few mixers use solid fuel. In terms of fuel combustion efficiency, gas fuel has the highest combustion efficiency, high calorific value and relatively stable combustion, but the cost of gas fuel is higher than that of liquid fuel, so it is more suitable for small and medium-sized mixing plants. Although the combustion calorific value of solid fuel is relatively high, its stability is poor, accidents are easy to occur, and the temperature control of solid fuel mixer is difficult. Therefore, solid fuel is generally not used as the main fuel of mixer. Liquid fuel has high calorific value, low impurity content, good controllability, and the cost is far lower than that of gaseous and solid fuel. It is very suitable for asphalt mixing plant. There are two kinds of liquid fuels commonly used in asphalt mixing plant: diesel and heavy oil. The cost of diesel is high, while the cost of heavy oil is low and the calorific value is relatively high, which can meet the requirements of the mixer. The mixing plant can use heavy oil as the main fuel to improve the operation efficiency of the mixer and reduce the operation cost of the mixer.
3. Adjust the fuel atomization state
The combustion efficiency of fuel oil is directly related to the atomization effect of fuel oil. Only when the fuel oil mist is stable and the air flow is stable, the working efficiency of fuel oil can reach the highest and the burner can burn fully. Ensure that the oil supply pressure and return pressure are stable, and the change of oil supply can be obtained through the setting and adjustment of return pressure. The atomization state of fuel oil is affected by fuel oil variety, air oil ratio, air flow and other factors. Generally speaking, the mixer has been adjusted to the best atomization state when leaving the factory, but after a long time of operation, the impurities in the fuel may block the nozzle and affect the atomization effect of the fuel. In order to keep the burner in the best working state, the staff of the mixing plant can install a filter in front of the booster pump of the mixer to reduce the probability of impurities entering the nozzle, Improve fuel combustion efficiency. In addition, clean the fuel injection nozzle of the burner regularly to prevent blockage of the fuel injection nozzle of the burner.